Stainless steel, an iron-based alloy known for its excellent corrosion resistance and durability, is widely used in various industries, including food processing, construction, medical devices, and more. However, there’s often confusion about whether stainless steel is magnetic. While some believe that stainless steel could be magnetic due to its iron content, the truth is more nuanced. This guide delves into the magnetic properties of different types of stainless steel, explaining why some are magnetic while others are not, and why understanding these properties is crucial for various applications.
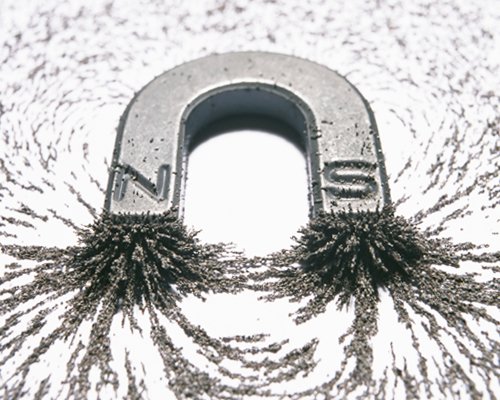
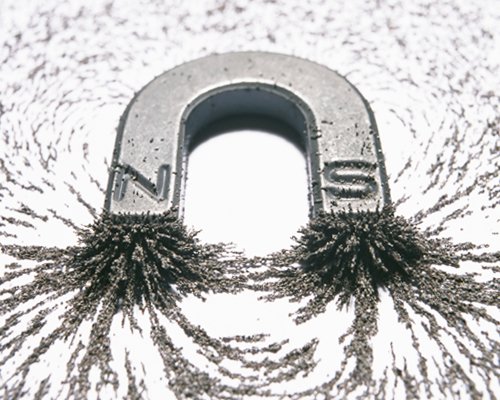
Understanding the Basics: What Makes Stainless Steel Magnetic?
To determine whether stainless steel is magnetic, two primary conditions must be met:
- Iron Content: The alloy must contain iron, a naturally magnetic element.
- Crystal Structure: The crystal structure of the alloy must be arranged in a ferritic or martensitic structure to exhibit magnetism.
Stainless steels are generally categorized based on their crystal structure and composition into austenitic, ferritic, martensitic, duplex, and precipitation-hardened types. These categories influence whether the stainless steel is magnetic.
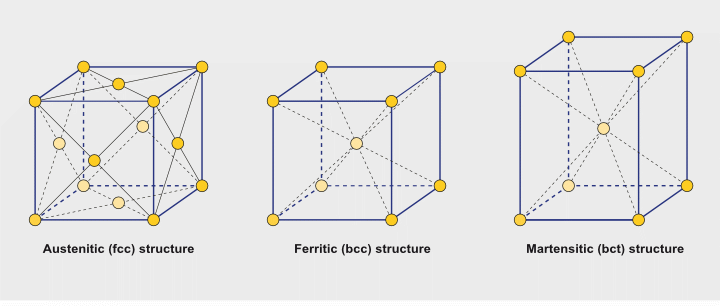
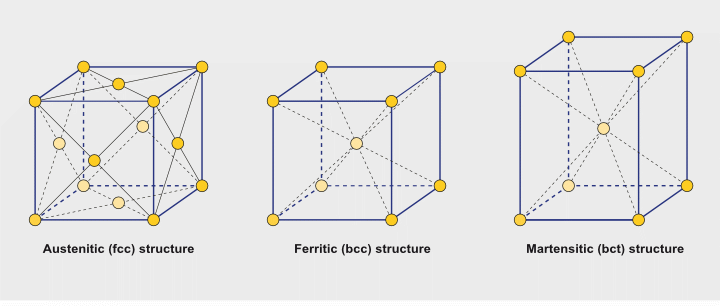
Austenitic Stainless Steels: Generally Non-Magnetic
Austenitic stainless steels, such as grades 304 and 316, are the most common types used in various applications. These steels have a face-centered cubic (FCC) crystal structure, which is stabilized by nickel and makes them generally non-magnetic in their annealed state.
However, austenitic stainless steels can become slightly magnetic through:
- Cold Working: Mechanical deformation processes, such as bending, rolling, or hammering, can alter the crystal structure, inducing the formation of martensite, a magnetic phase of iron.
- Welding and Thermal Treatments: High temperatures and stresses applied during welding or thermal treatments can cause localized transformation of austenite to martensite, resulting in slight magnetism in those areas.
This slight magnetism is typically observed at the edges or surfaces that have been mechanically worked, such as the edge of a sheet.
Ferritic Stainless Steels: Magnetic by Nature
Ferritic stainless steels, such as grades 409, 430, and 439, are magnetic. They have a body-centered cubic (BCC) crystal structure, similar to that of pure iron, which gives them their magnetic properties. Ferritic stainless steels contain high amounts of iron and have little or no nickel, resulting in a structure that is magnetic by nature. These steels are commonly used in automotive applications, kitchenware, and industrial equipment.
Martensitic Stainless Steels: Strongly Magnetic
Martensitic stainless steels, including grades 410, 420, and 440, are also magnetic. These steels have a body-centered tetragonal (BCT) crystal structure and are typically hardened through heat treatment. The high iron content in martensitic stainless steels and their unique crystal structure contribute to their strong magnetic properties. They are often used in applications requiring high strength and wear resistance, such as cutlery, surgical instruments, and valves.
Duplex and Precipitation-Hardened Stainless Steels: Varying Magnetic Properties
Duplex stainless steels combine austenitic and ferritic structures, offering a balance of good strength and corrosion resistance. They usually exhibit some degree of magnetism due to the presence of ferritic phases.
Precipitation-hardened stainless steels achieve high strength through heat treatment and typically exhibit magnetic properties. The extent of magnetism depends on the specific alloy composition and heat treatment applied.
Why Some Stainless Steels Exhibit Weak Magnetism
Although austenitic stainless steels like 304 and 316 are generally non-magnetic, they can exhibit weak magnetism due to several factors:
- Cold Working: Mechanical deformation can cause microscopic structural changes, converting some austenitic phases into martensitic phases, which are magnetic. This is especially noticeable in thin sheets or deeply processed parts.
- Stress-Induced Martensite: Mechanical stress during production, especially under high-stress conditions, can induce the transformation of austenite into martensite, causing localized magnetism.
- Phase Changes from Welding and Heating: Welding or exposure to high temperatures can lead to phase changes in specific areas, resulting in weak magnetism around the welds or heat-affected zones.
- Residual Martensite: Even without cold working or stress, some batches may contain residual martensite due to casting and annealing processes, leading to weak but generally unnoticeable magnetism.
Practical Implications of Magnetic Properties in Stainless Steel
The magnetic properties of stainless steel can significantly impact its performance and suitability for specific applications. Here are some practical implications:
- Fabrication and Welding: Magnetic materials can interfere with arc stability during welding and complicate fabrication processes, affecting the final product’s quality.
- Separation and Removal: In food processing and pharmaceutical industries, stainless steel particles can contaminate products. Magnetic separators are used to remove these particles. Ferritic and martensitic stainless steels, being magnetic, are easier to remove than austenitic ones.
- Electrical Applications: In applications involving electricity, magnetic properties can influence how electric currents behave, potentially causing unintended interference or losses.
Accurate Identification Methods for Stainless Steel
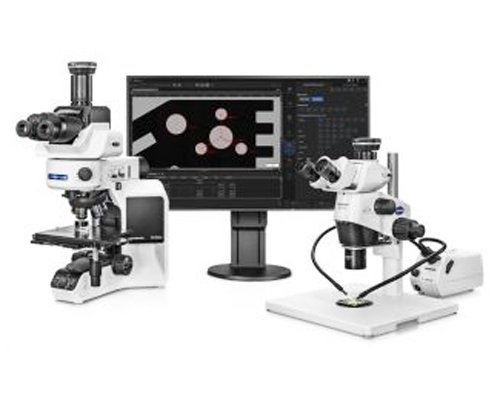
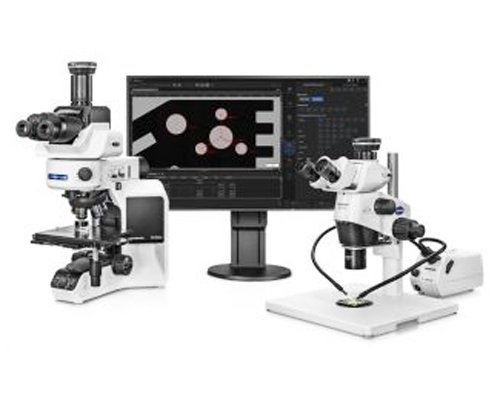
To accurately identify the type of stainless steel and its magnetic properties, relying on scientific methods is essential:
- Chemical Composition Analysis: Using spectrometric equipment to analyze the alloy’s composition ensures it meets specific standards, such as those for SUS304, which contains 18% chromium and 8% nickel.
- Nitric Acid Spot Test: Applying dilute nitric acid to the stainless steel surface can help identify the alloy. SUS304, for instance, will not react, while lower-quality steels may corrode or discolor.
- X-Ray Fluorescence (XRF) Spectroscopy: This non-destructive testing method analyzes the alloy’s surface to determine its composition, offering quick and accurate results.
- Corrosion Resistance Testing: Conducted in laboratories, these tests simulate various environments to verify the alloy’s durability and suitability for specific applications.
- Metallographic Microscope Analysis: Examining the internal structure of the alloy under a microscope can confirm its identity and guide further processing.
- Visual Inspection: While not conclusive, the smooth surface and high gloss of austenitic stainless steels, such as SUS304, can provide initial clues about their composition.
Conclusion
Understanding the magnetic properties of different types of stainless steel is crucial for selecting the right material for your application. While ferritic and martensitic stainless steels are magnetic due to their crystal structures, austenitic stainless steels like 304 and 316 are generally non-magnetic but can become slightly magnetic under certain conditions. Recognizing these properties helps in optimizing material selection, ensuring optimal performance, and avoiding potential issues related to unwanted magnetism in various industrial and commercial applications.
Saryee Belting’s Stainless Steel Conveyor Belts: The Top Choice for Quality and Reliability
As a leading manufacturer of stainless steel conveyor belts, Saryee Belting leverages years of production experience and technical expertise to deliver top-quality stainless steel products to customers worldwide. Our stainless steel conveyor belts are designed to meet international standards and offer exceptional adaptability across various applications.
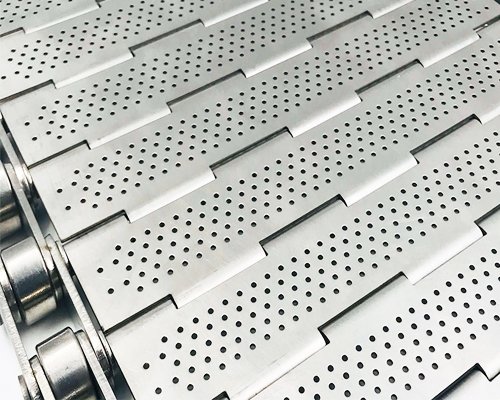
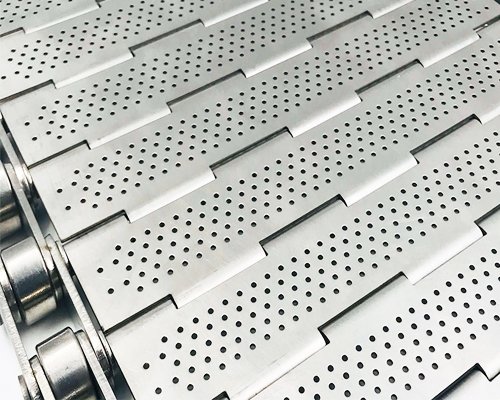
Key Features of Saryee Belting’s Stainless Steel Conveyor Belts
- Superior Corrosion Resistance: Our SUS304 stainless steel conveyor belts perform excellently in harsh environments, providing robust corrosion resistance and an extended service life.
- Exceptional Strength and Durability: Our conveyor belts maintain excellent physical properties in both high-temperature and low-temperature conditions, making them ideal for demanding industries such as food processing, chemicals, and pharmaceuticals.
- Precision Manufacturing: Utilizing advanced manufacturing techniques, our conveyor belts are produced with fine surface treatments and precise dimensions, ensuring each belt meets the stringent requirements of our customers.
- Wide Range of Applications: Beyond food processing, our stainless steel conveyor belts are widely used in various industries, including electronics, pharmaceuticals, chemicals, and automotive manufacturing.
Saryee Belting is committed to providing high-quality, reliable solutions tailored to the specific needs of different industries, ensuring optimal performance and customer satisfaction.