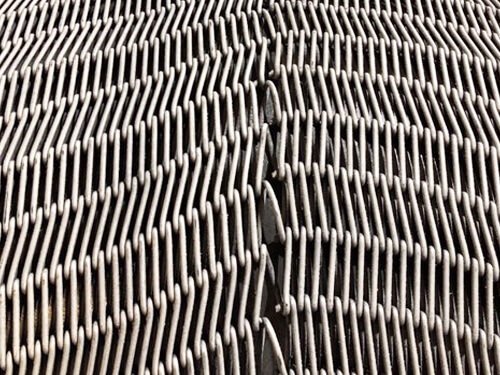
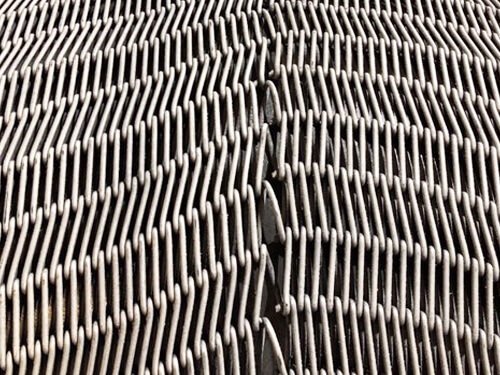
Naturally, every conveyor belt, including metal conveyor belts, has a limited lifespan. Yet, it’s noteworthy that most conveyor belts don’t reach the end of their lifespan due to wear and tear. Rather, failures often stem from factors unrelated to the belt’s durability or longevity. These failures, discussed below, lead to significant downtime, translating to missed opportunities, decreased production, and diminished profits.
- Material Buildup and Contamination: Accumulation of materials on the conveyor belt or its components can lead to increased friction, reduced efficiency, and eventually belt damage or failure. This buildup can include dust, dirt, debris, and spillage from transported materials.
- Mechanical Wear and Tear: Continuous operation can cause wear and tear on conveyor belts and their components such as rollers, idlers, pulleys, and splices. Over time, this wear can result in belt misalignment, tracking issues, and eventual failure if not addressed promptly.
- Belt Misalignment and Tracking Issues: Improper alignment of the conveyor belt can cause it to veer off course, leading to friction, rubbing against components, and potential damage. Tracking issues can arise from misaligned rollers, improper tensioning, or uneven loading of materials onto the belt.
- Overloading and Material Jamming: Exceeding the conveyor’s designed capacity or sudden surges in material flow can overload the system, leading to strain on the belt and its components. Material jamming can occur at transfer points, bends, or due to irregularly shaped objects, causing stoppages and potential damage.
- Belt Splicing and Joint Failure: Conveyor belts are often composed of multiple sections joined together by splices. Poorly executed splices or joint failure due to excessive tension, corrosion, or mechanical stress can result in downtime and require repair or replacement.
- Environmental Factors: Extreme temperatures, humidity, and exposure to harsh chemicals or abrasive materials can accelerate wear and degradation of conveyor belts and components, leading to premature failure and downtime.
- Lack of Maintenance and Inspection: Inadequate maintenance practices, including infrequent inspections, lubrication, and cleaning, can allow minor issues to escalate into major problems. Regular maintenance is crucial for identifying and addressing potential issues before they cause downtime.
- Equipment Malfunction and Breakdown: Mechanical failures in conveyor components such as motors, bearings, drives, and control systems can result in unexpected downtime. These failures may stem from manufacturing defects, inadequate maintenance, or aging equipment.
- Power Outages and Electrical Issues: Dependence on electrical power for conveyor operation makes the system vulnerable to outages, voltage fluctuations, and electrical faults. Backup power systems and surge protection measures can help mitigate these risks.
- Operator Error and Training: Inadequate operator training or human error during operation, maintenance, or troubleshooting can contribute to conveyor downtime. Proper training programs and clear operational procedures are essential for minimizing these risks.
Addressing these causes requires a comprehensive approach that encompasses proactive maintenance, regular inspections, training programs, and investment in robust equipment and operational practices to minimize downtime and maximize conveyor uptime and efficiency.